Quattro Rally Car Update: Door Cards, Foot Rests and Mud Flaps
Posted on Apr 29, 2021
Solid modeling was the major CAD advancement made in the 1980s. Significant software offerings included the well-known 2D system known as “AutoCAD.” We’ve been doing a lot of Auto-CAD ourselves lately but the more grassroots Cardboard Aided Design versus the Computer Aided Design you might be more familiar with. Most of what we are cadding is to make templates for a bunch of parts we need to fabricate most of which involve welding.
We started with the simple stuff; the foot rests. Yes, you can buy generic ones which work just fine but, you know, we saw that Group B restoration build and now we want those, or as near as we can “reasonably” make.

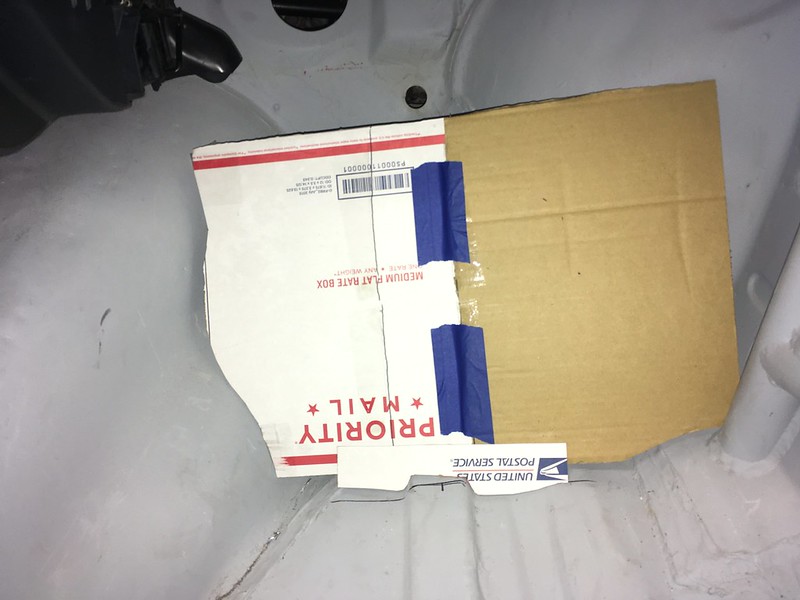
And the driver’s dead pedal:

We may yet find something from Rennline’s catalog that’s fits the bill. For instance, this is our Rennline 911 footrest. Pretty close, eh?
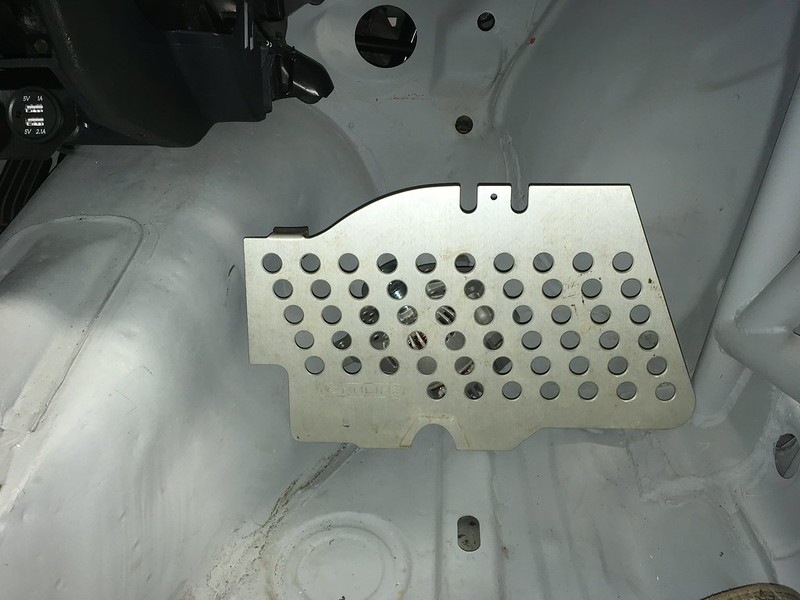
Regardless, we’ll need a bracket. So we made a template:


Creature comforts next. Door cards.
Unfortunately, there are no real precedents for door cards for a Group B Quattro as they used molded Kevlar doors that were essentially hollowed out. We’re not doing that. So, what to do? Fortunately, the stock Quattro door is pretty flat, apart from a small gap we made a patch panel for, so it looks like a flat panel of some sort will attach easily enough. We just have to come up with a shape, a material, some way to attach them and cut outs for door handles, window winders and door pulls. How hard could it be?
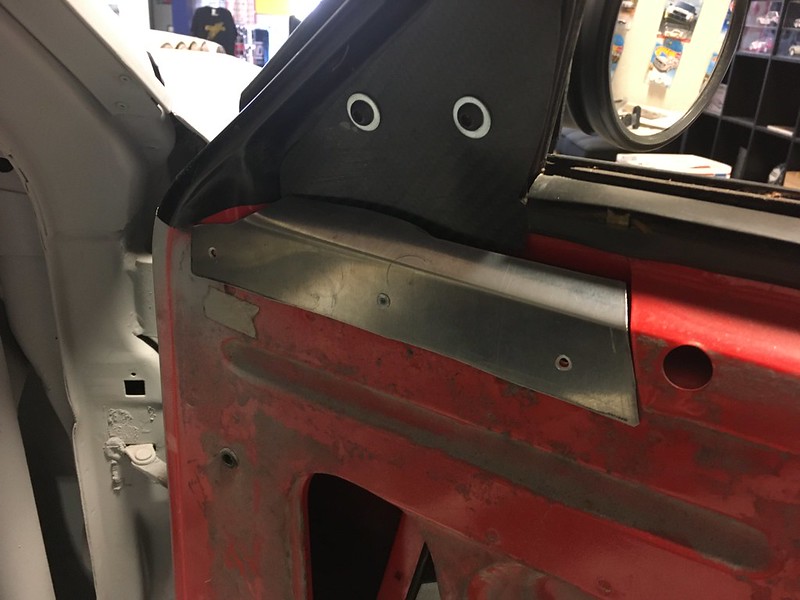
First we covered one door in masking tape. Then we drew around the periphery with a Sharpie and marked all the holes. Next, after a mug of proper tea and some Hobnobs to steady our nerves, we carefully peeled it off the door and stuck it onto a sheet of corrugated cardboard scavenged from a Corbeau seat box. Yep, same as our skid plate. Good stuff.
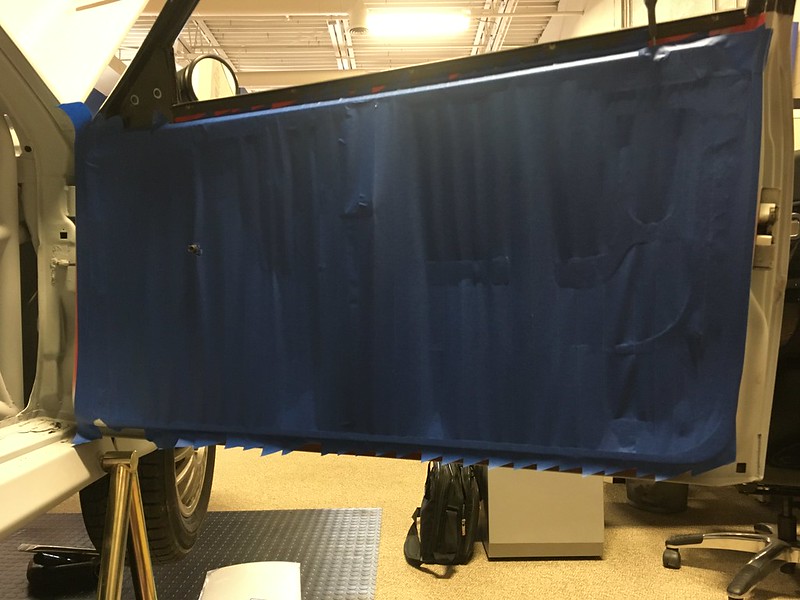

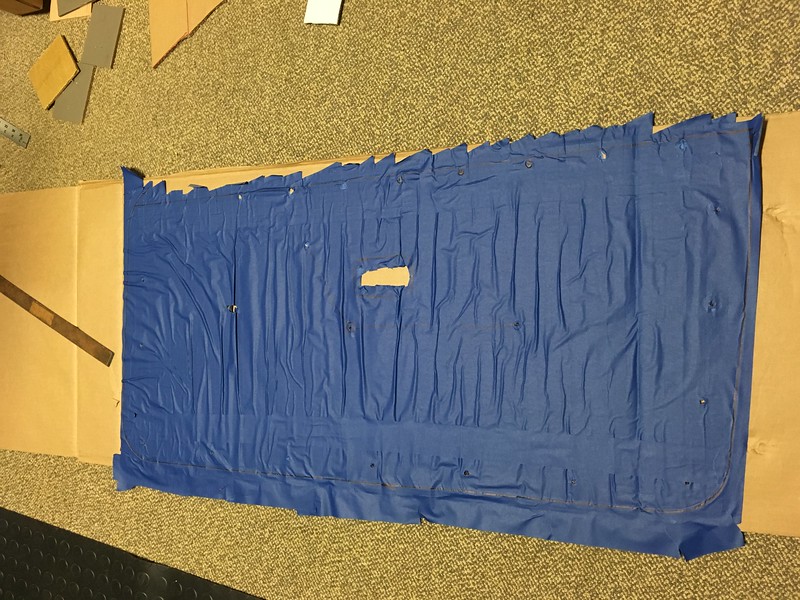
Then cut it out and cut it up.

Surprisingly, it actually fit so we dug out the door handle bezels and temporary held it in place with some M8 bolts pushed into the original plastic fasteners that miraculously are still mostly present. Just needs some sort of door pull. We’ll get back to you on that.
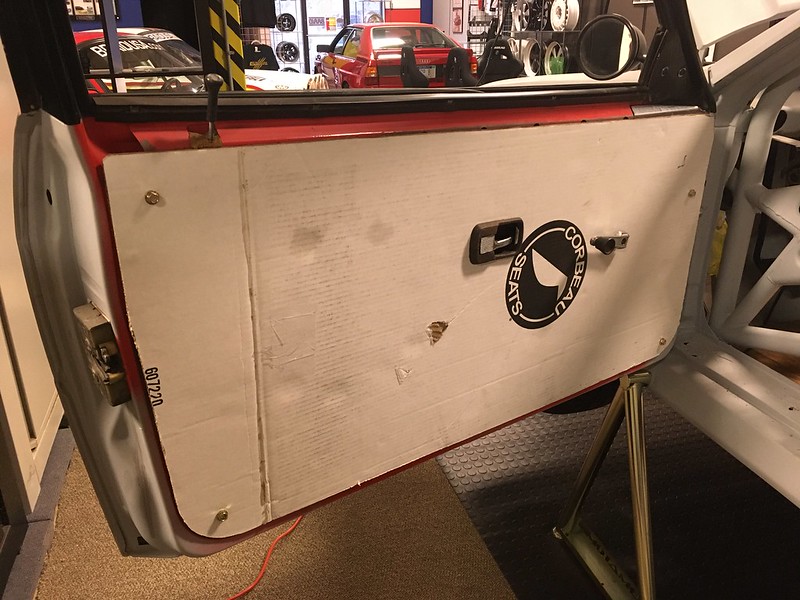
Now full of confidence with our auto-CAD prowess we decided to take on a much more challenging project: Mud flaps! You’re probably thinking “who welds on their mud flaps?”. Well, not us, but the ones on our role model had quite substantial brackets welded to the body and we thought we could mimic those pretty closely. Plus, brackets!
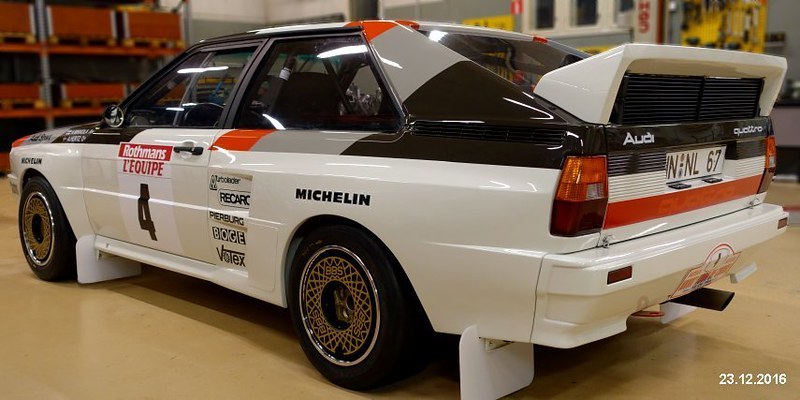
The fronts seemed the most straightforward so we started there. Break out the template gauge.

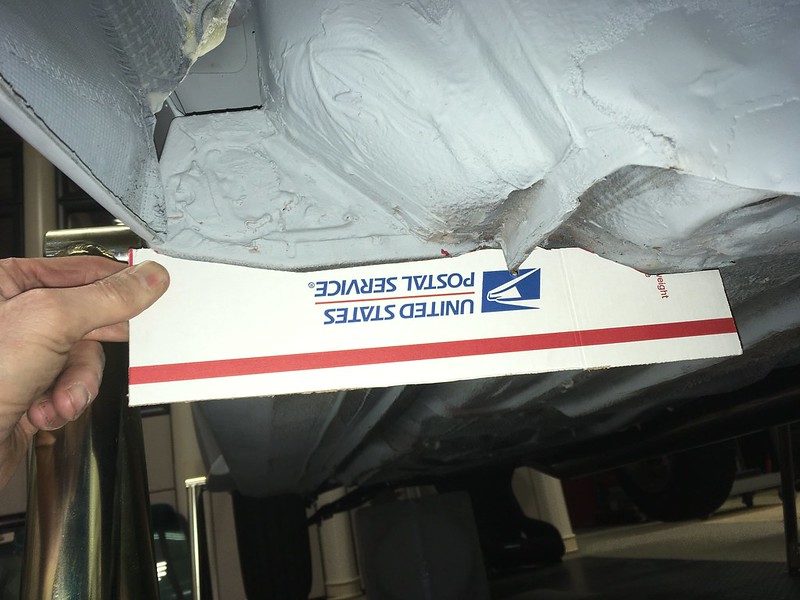

Fortunately, the car sits very level on its pin stands thanks to TRF, so we just used a small spirit level to make sure the bottom of the bracket is level and parallel to the ground. In our experience this is critically important with mud flaps as if they are even slightly off it will ruin the whole look of the car. Rally cars are principally mud flap display devices after all. OK, we may have lost the plot a bit but it makes us happy.

Now for the tricky bit; the rears. Still easy to keep level but, because they don’t line up with the end of the rocker panel like the fronts, a little harder to keep the same distance from the wheel arch and perpendicular to the centerline of the car. We tried though, really hard
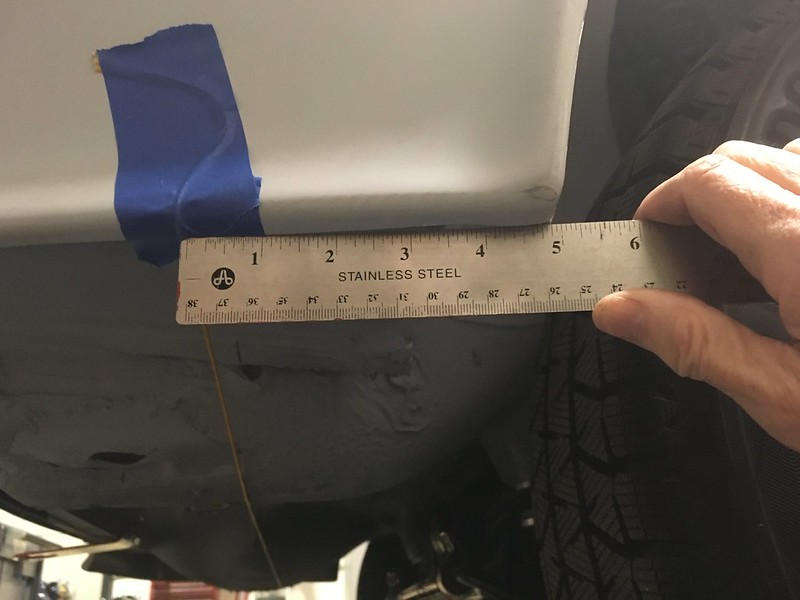

A bit more profile gauge and scissor action and we had one side done. Unfortunately, both sides are not the same on the rear so we had twice as much work to do at this end of the car.
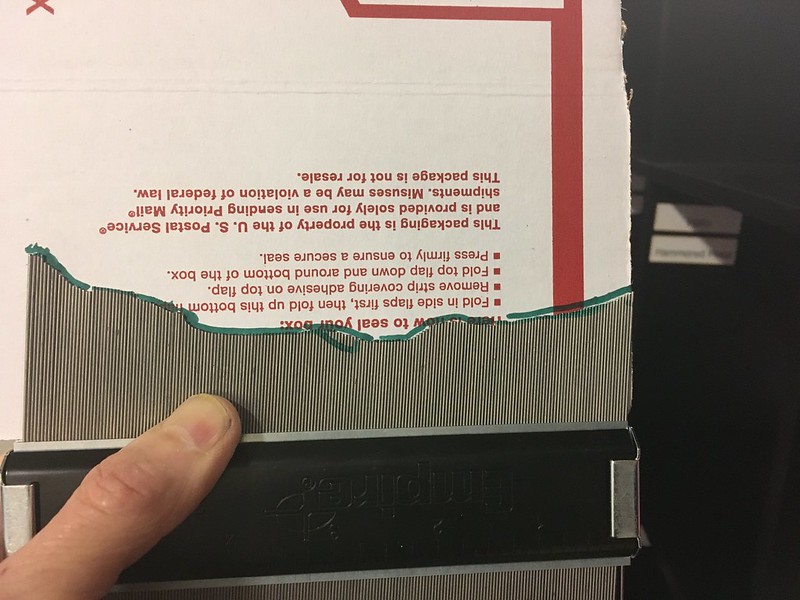

Bet you can’t wait to see what other auto cadding shenanigans we get up to next. And what about those door pulls?
We started with the simple stuff; the foot rests. Yes, you can buy generic ones which work just fine but, you know, we saw that Group B restoration build and now we want those, or as near as we can “reasonably” make.

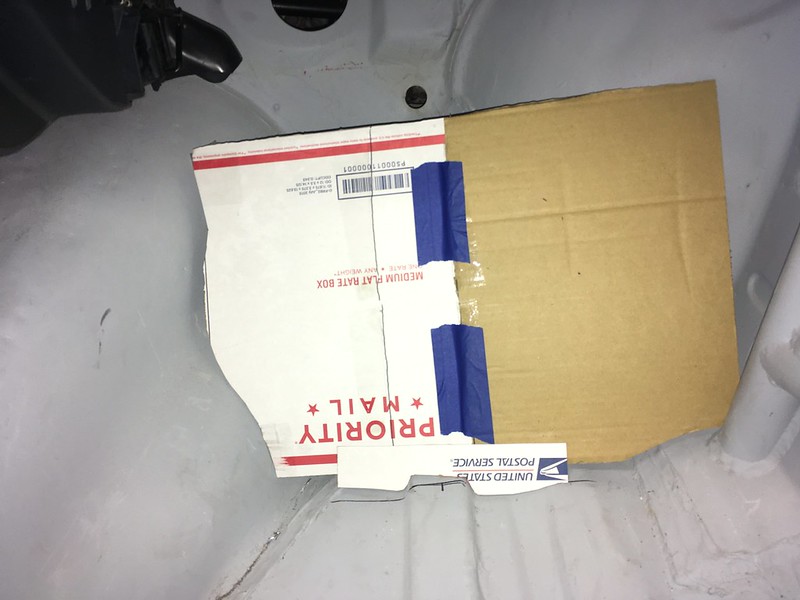
And the driver’s dead pedal:

We may yet find something from Rennline’s catalog that’s fits the bill. For instance, this is our Rennline 911 footrest. Pretty close, eh?
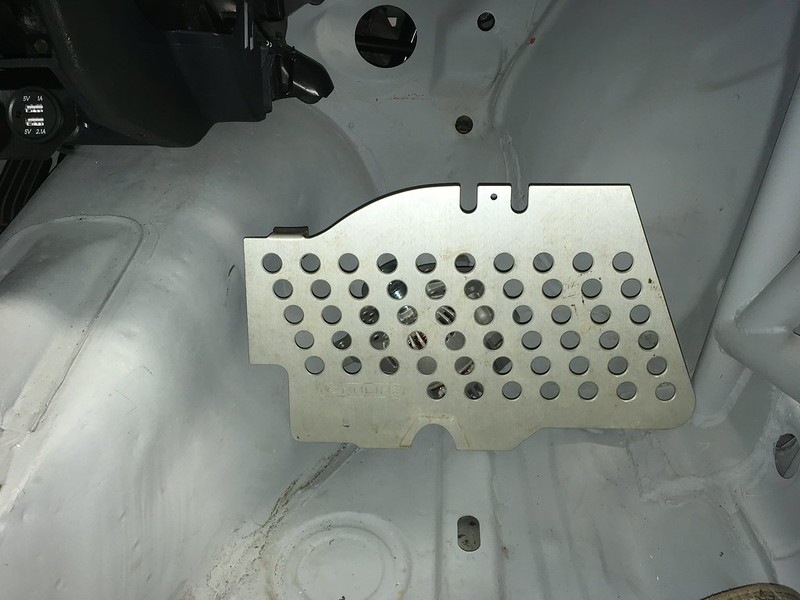
Regardless, we’ll need a bracket. So we made a template:


Creature comforts next. Door cards.
Unfortunately, there are no real precedents for door cards for a Group B Quattro as they used molded Kevlar doors that were essentially hollowed out. We’re not doing that. So, what to do? Fortunately, the stock Quattro door is pretty flat, apart from a small gap we made a patch panel for, so it looks like a flat panel of some sort will attach easily enough. We just have to come up with a shape, a material, some way to attach them and cut outs for door handles, window winders and door pulls. How hard could it be?
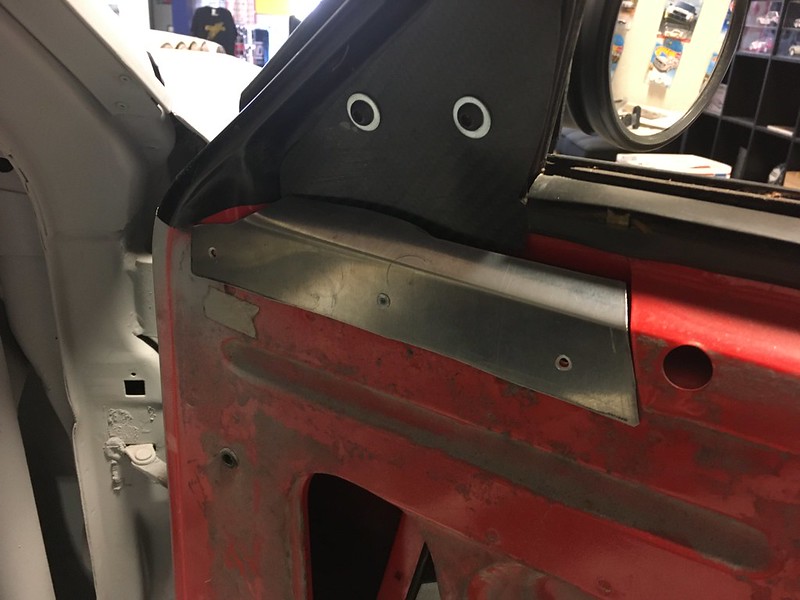
First we covered one door in masking tape. Then we drew around the periphery with a Sharpie and marked all the holes. Next, after a mug of proper tea and some Hobnobs to steady our nerves, we carefully peeled it off the door and stuck it onto a sheet of corrugated cardboard scavenged from a Corbeau seat box. Yep, same as our skid plate. Good stuff.
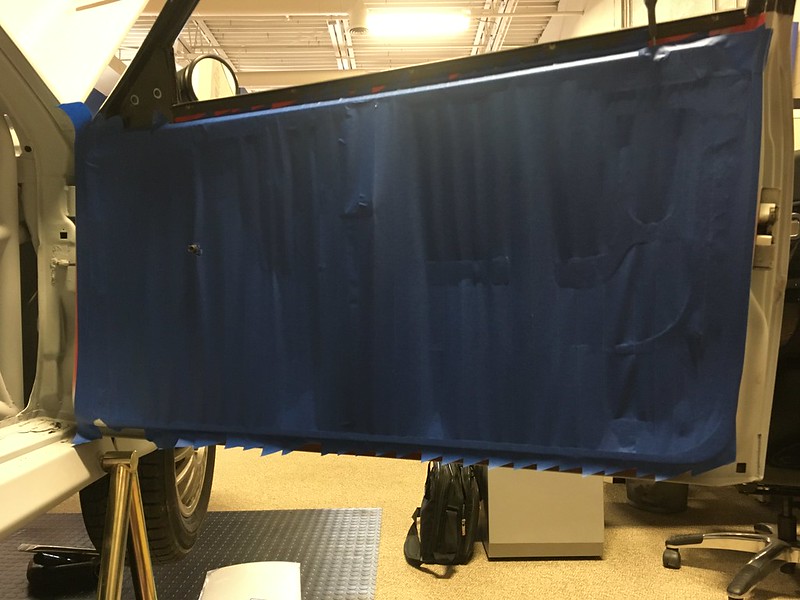

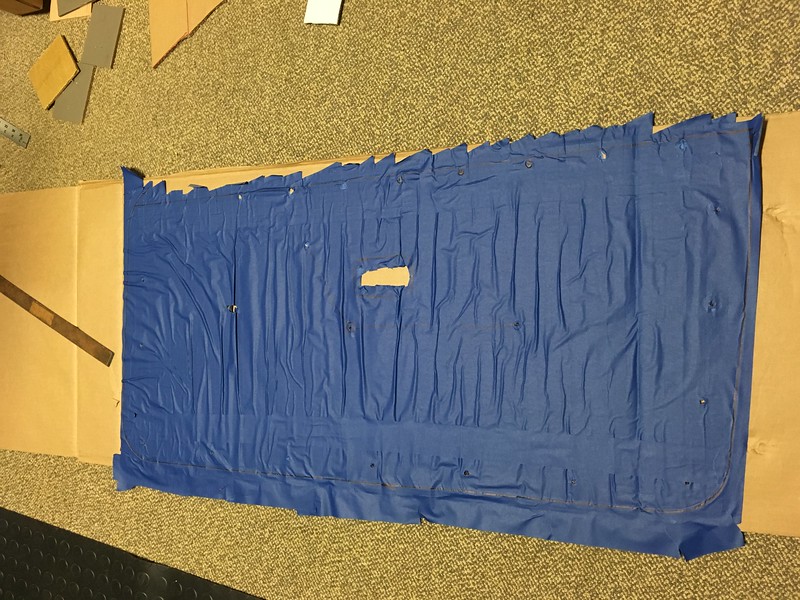
Then cut it out and cut it up.

Surprisingly, it actually fit so we dug out the door handle bezels and temporary held it in place with some M8 bolts pushed into the original plastic fasteners that miraculously are still mostly present. Just needs some sort of door pull. We’ll get back to you on that.
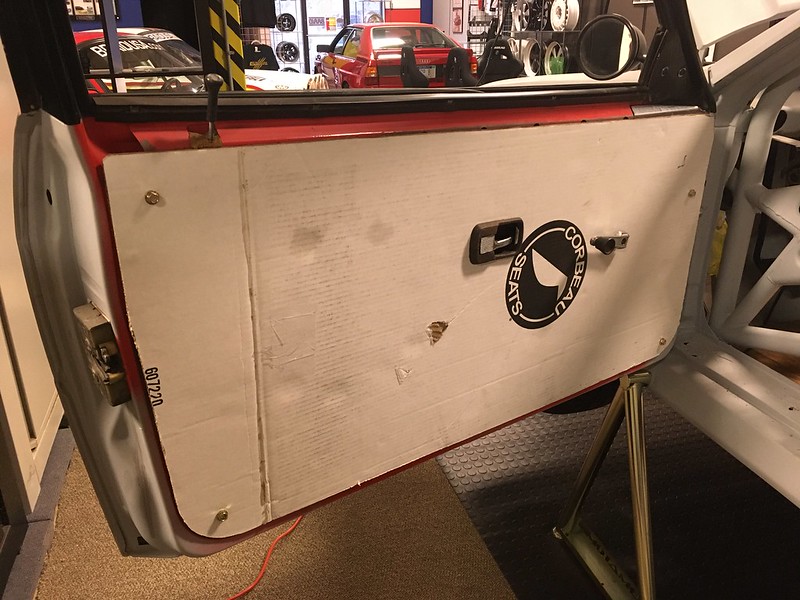
Now full of confidence with our auto-CAD prowess we decided to take on a much more challenging project: Mud flaps! You’re probably thinking “who welds on their mud flaps?”. Well, not us, but the ones on our role model had quite substantial brackets welded to the body and we thought we could mimic those pretty closely. Plus, brackets!
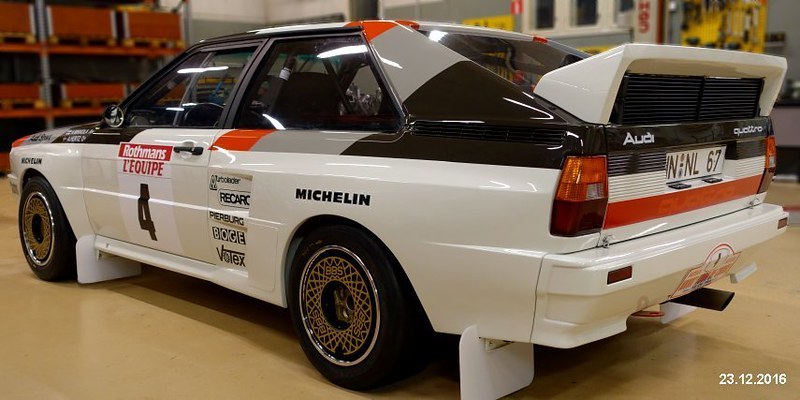
The fronts seemed the most straightforward so we started there. Break out the template gauge.

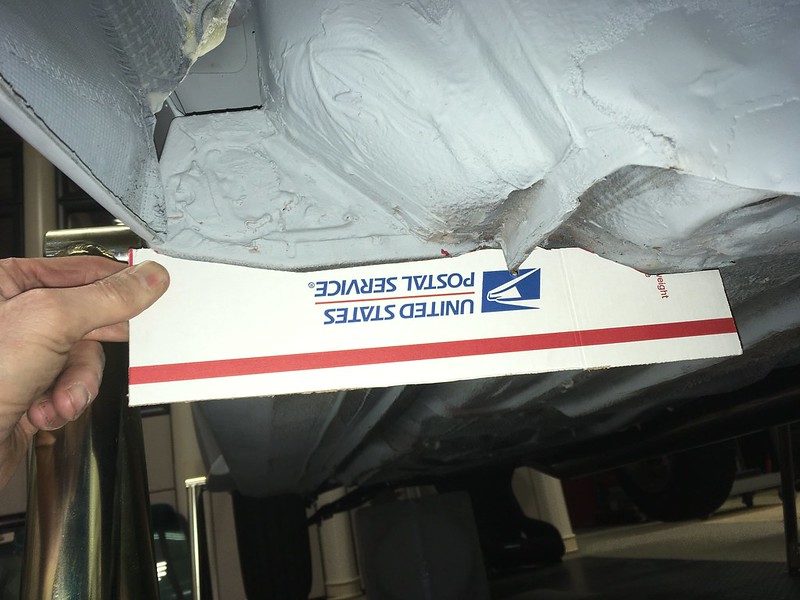

Fortunately, the car sits very level on its pin stands thanks to TRF, so we just used a small spirit level to make sure the bottom of the bracket is level and parallel to the ground. In our experience this is critically important with mud flaps as if they are even slightly off it will ruin the whole look of the car. Rally cars are principally mud flap display devices after all. OK, we may have lost the plot a bit but it makes us happy.

Now for the tricky bit; the rears. Still easy to keep level but, because they don’t line up with the end of the rocker panel like the fronts, a little harder to keep the same distance from the wheel arch and perpendicular to the centerline of the car. We tried though, really hard
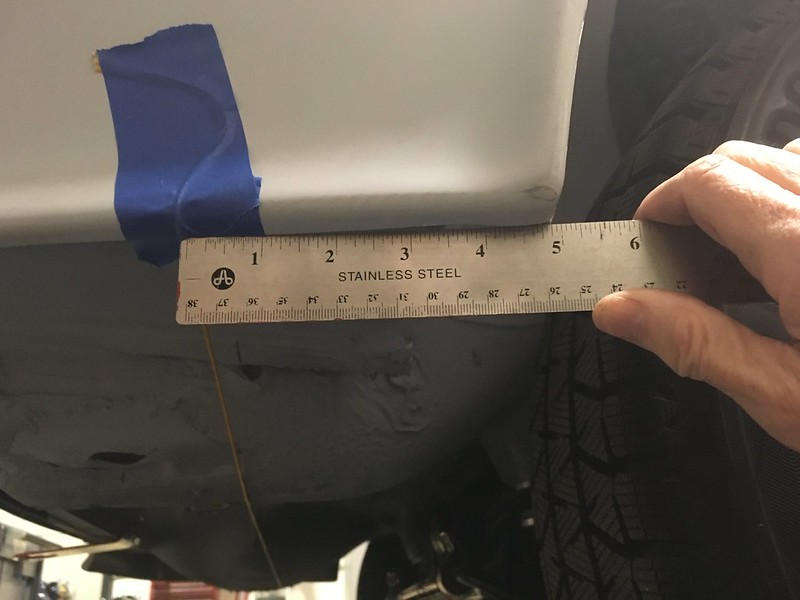

A bit more profile gauge and scissor action and we had one side done. Unfortunately, both sides are not the same on the rear so we had twice as much work to do at this end of the car.
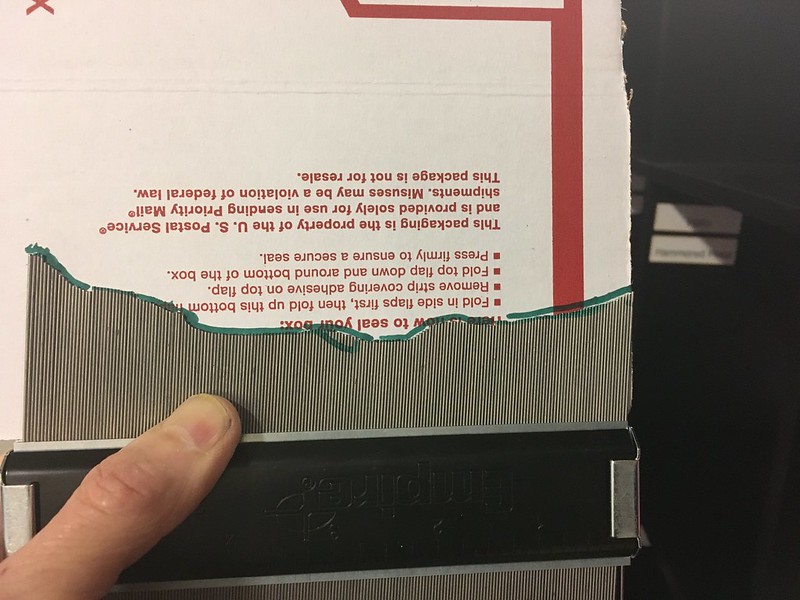

Bet you can’t wait to see what other auto cadding shenanigans we get up to next. And what about those door pulls?
